Windows & Doors

Considering the broad commercialization of insulating glass units in the early 70s, adhesives and sealants were always an essential ingredient in the manufacture of insulating glass and window units.
The usage has been intensified by structural glass bonding, the so-called “structural glazing”. Today our modern skyscrapers, office buildings and shopping malls are all dominated by glass facades and glass curtain walls. With ever more imposing customized architectural designs the dominance of glass is increasing.
In addition to the aesthetic design, structural glazing must satisfy functional properties like thermal insulation, temperature resistance as well as long-term durability. Only structural bonding, by using of high-performance adhesives makes this possible.
Get a Quote for a Window and Door ApplicationAdhesives and sealants need to be very accurately processed and precisely applied in order to ensure an optimum glass bonding and sealing.
Constantly increasing demands for higher productivity and quality require reliable processing equipment and an appropriate quality control.
As a leading supplier of metering and mixing systems, Kirkco has supported the glazing industry since its foundation.
We offer a wide range of products to process liquid materials in different applications taking the manufacturing environment and local requirements into account. From simple manual applications to complete solutions with fully automated robot cells with integrated process control – complemented by outstanding service and spare parts availability.
As a partner of major adhesive manufacturers, we help to optimize processes and find new solutions for the market – for the benefit of all our customers.
Since 1985 Kirkco has been serving the window, door, and insulated glass industries by providing innovative sealant dispensing solutions and products with superior customer service.
Kirkco is committed to providing turnkey dispensing solutions to meet the needs of developing cutting-edge adhesive technologies. By providing unique processes solutions and un-matched new product developments, we are continuously working towards the purpose of reducing cost, and improving quality for the manufacturer and the consumer.
Kirkco will continue to provide outstanding support and service to our customers and our adhesive and sealant, manufacturing and distribution partners.
Exceptional service, innovative adhesive and sealant dispensing solutions and a comprehensive equipment offering will continue to build Kirkco's reputation as leader in the building products industry.
Edge Sealant Dispensing and Glazing
Ecostar EVO Series »
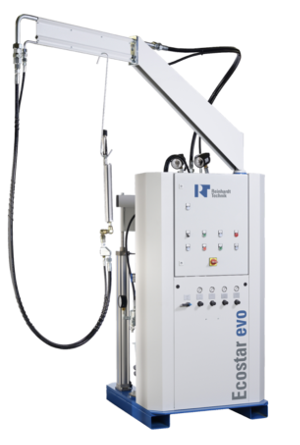
The Ecostar EVO range of machines are high quality metering and mixing systems, specifically developed for processing and applying viscous two component edge sealants in the glazing industry.
Polyurethanes, polysulphides and silicones can all be successfully applied with this versatile range of machines. Making use of a simple variable ratio mechanical lever system, the metering ratio can be easily adjusted between 8:1 and 15:1 by volume, meaning that you are not tied to just one material manufacturer as you might be with a fixed ratio machine.
Smooth running powerful, hydraulically driven versions are available as well as pneumatically driven machines, whilst the hardener component can be supplied as either a paste or a liquid. Just tell us your needs and we will build the perfect machine for your production requirements.
Features
- Compact, lightweight, portable
- Reliable mechanical lever system
- Variable mixing ratio
- Static mixing system
- Continuous material output
- High production rates
- No solvent flushing
Conti Flow Versa »
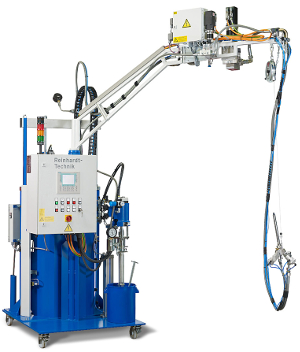
The Conti Flow Versa series proportioner synchronizes the volume of the two components through two precisely sized positive displacement gear pumps. Pumps are coated with protective material to prevent ware due to fillers. The fluids are delivered through hoses to a mixer assembly.
Selecting from standard pump availability determines the ratio range of the machine. A programmable electronic control allows for an adjustable variable ratio within a given range. With the optional ratio monitoring package, the computer will self-adjust automatically.
Features
- Versatile & flexible for demanding workspaces
- High metering accuracy due to short distance from metering to dispensing
- Highly comfortable operation with flexible boom and balancer support
- Different options & features are configurable to meet requirements
- PLC controlled
- Low level alarm
- Pot life alarm
- Continuous pressure monitoring
Insulated Window Applications & Adhesives
Insulating Glass (IG) [Secondary Sealing]
Insulating glass (IG) units consist of two or more glass panes which are separated along the perimeter by a spacer and sealant system. The cavity between the panes of glass may be filled with dry air or an inert gas. Many types of glass can be used including laminated glass, coated glass or spandrel glass. These components are selected to meet the specific coloration, reflectivity, light transmission and sound transmission requirements of the IG unit. Insulating glass is also used in silicone structural glazing which is a method utilizing silicone adhesive to attach glass to the structure of a building.
Structure Glazing [Bonding Brackets to Glass]
Structural glazing is a method utilizing an adhesive to attach glass, metal, or other panel material to the structure of a building. Wind load and other impact loads on the façade are transferred from the glass or panel, through the structural sealant to the structure of the building. The sealant must maintain adhesive and cohesive integrity as the façade is subjected to wind load and thermal stresses.
Direct Glazing [Bonding Glass Inside Window Frame]
Bonded IG glass units in the glazing rebate for all window and door sash sizes prevent the thermal bridge that is typical for conventional windows
Two-Part IG Sealants
Polyurethane
Polyurethane Insulating Glass Sealants are one of the three main adhesive technologies for the insulated glass units (IGU) manufacturing process. There have been dozen of formulations created to accommodate the various manufacturing needs of IG customers. These formulas can be modified for cure speed and thickness to meet the specifications of production specifications.
Polyurethane has shown to have poor UV resistance and moisture resistance, but superior adhesion and flexibility, and greater durability than other two-component IG technologies. Polyurethane can be used in single or duel seal systems.
Polysulphide
Polysulfide dominates insulated glass secondary seal application, followed by relatively small shares for Polyurethane (PUR), Silicone and Hot Melt sealants. Polysulfide has good UV and chemical resistance, and can be used in single seal or dual seal system. Polysulfide based sealants for Insulted glass units (IGU) are very tolerant against mistakes in production and forgive variations in temperature and mix ratio to a large extent.
Silicone
Silicone IG Sealant offers some important performance advantages, such as excellent UV and weathering resistance, structural integrity, excellent long-term durability, excellent unprimed adhesion and a wide service temperature range. Because it doesn’t contain solvents, it shrinks much less than polysulfide sealants during cure.
One-Part Curable IG Sealants
One component (one-part) curable Insulating Glass Sealants manage to combine the ease of application of Hot Melt Butyl with the long-term performance characteristics of Polyurethane to produce among the highest performing insulating glass sealants for window glazing and insulted glass unit (IGU) applications.
Hot Melt Butyl
Hot Melt Butyl IG Sealants have consistently proven to be the high performing sealant in the residential window glazing and insulated glass market. Hot melt butyls have excellent moisture vapor resistance rates. Since they are thermal plastic in nature they do not require a cure time as Silicone, PUR, and PS.
Primary Sealants - CPS, NPS
Polyisobutylene (PIB) is used as the primary moisture barrier seal in all dual-seal insulated units. While PIB has excellent MVT (moisture vapor transmission), it lacks mechanical strength and needs to be used in conjunction with a secondary edge sealant such as polyurethane, Polysulfide or silicone.
Warm Melt PIB sealants are applied at reduced temperatures, translating into energy cost savings. Easy dispensing provides improved quality and increased production rates as well.
The Visco Star bulk unloaders with warm melt configuration is used to efficiently dispense a wide range of warm applied PIB sealant materials. Available with flow boost technology to Improve product quality with dispensing accuracy and precision adhesive application.