Tilting at Windmills
By Bob Jones
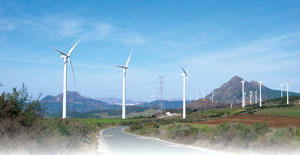
Whilst the demand for energy increases throughout the world, concern over traditional methods of generating electrical power has begun to foster a move towards renewable energy sources. The use of wind, water, and solar power are already widespread, but the mass production of electricity using renewable energy sources has become popular only recently, reflecting the major threats of climate change, concerns about the exhaustion of fossil fuels and the environmental, social and political risks of extensive use of fossil fuels and nuclear power.
Get a Quote for a Wind Energy ApplicationWind energy is abundant, renewable, widely distributed, clean, and mitigates the greenhouse effect if it is used to replace fossil-fuel derived electricity. Although current production accounts for less than 1% of worldwide electricity use and is still a relatively minor source of electricity for most countries, it accounts for 23% of electricity use in Denmark, 4.3% in Germany and around 8% in Spain. Globally, wind power generation more than quadrupled between 1999 and 2005 and is targeted to reach 12% of worldwide energy demand.
Wind power is now used in large-scale wind farms for providing power to national electrical grids both onshore and more recently offshore. Construction of the huge rotor blades used in the latest generation of wind generators is bringing with it new technical challenges, the production of which is a three-stage process.
Firstly, each glass reinforced plastic (GRP) blade is manufactured in two halves by the infusion of two component resin into the fiber matt. Secondly, the two halves are glued together with two component epoxy resin and finally, a gel coat system is applied to the outer surface of the blade. These processes may sound simple enough, but in reality the sheer scale of the rotor blades demands highly specialized metering, mixing and dispensing systems.
For example, the infusion process for a standard 50 meter long blade will take upwards of six hours to dispense and use around 1000 kg of resin, whilst 600 kg of resin is typically used for gluing the two halves together.
It was for these reasons that the Hilger u. Kern / Dopag Group has developed a new range of ELDO-MIX metering, mixing and dispensing systems especially for the purpose of producing rotor blades using the two-form construction technique.
ELDO-MIX Resin Infusion: Guaranteed Mix Ratio Accuracy
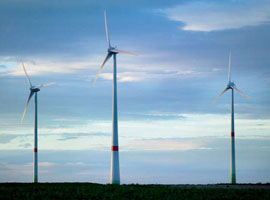
With worldwide electrical energy generated by wind power planned to reach 12% of total energy requirement by the year 2020, compared to the present 1%, it is clear that the production of wind generating equipment is set to soar.
Key components of this equipment are the rotor blades that turn the turbines. The fabrication of these glass reinforced plastic (GRP) rotor blades is quite a complex and specialized process. The production technique consists of three distinct stages. Firstly, most blades are manufactured from two halves, following which they are bonded together and finally they receive a smooth outer coat.
What follows is a brief insight into the first production stage where a vacuum supported infusion of a two component resin into fiber matting takes place. Since the operational efficiency of a windmill largely depends on the mechanical attributes of the rotor blades, one of the most important aspects of this process is the deviation from the selected mixing ratio, which must not exceed 3% during the entire time of the infusion process, which can typically take up to six hours.
The mixing ratio is capable of being checked after manufacture by means of a glass transition temperature test, which defines at which temperature the material has the highest deformation. However, not only is it vital to maintain a stable mixing ratio, but also the output rate must be adjustable during the metering process if required.
In order to attain these stringent requirements, the Hilger u. Kern / Dopag Group have developed a new ELDO-MIX metering and mixing system specifically for the vacuum supported infusion process that has been designed to have an accuracy of 1%, whilst the output rate is changeable in steps of 2% during production. Key components of this solution are the magnetically coupled axial piston pumps and an MR20 high speed integrated metering computer, with system monitoring functions and production data capture, whilst all the necessary interfaces to allow for integration into fully automated production processes, or a master computer exist as a standard function.
Demand from the marketplace dictates that mixing ratio flexibility is an equally important requirement and can be achieved with the ELDO-MIX by not only altering the frequency of rotation, but also by adjusting the stroke length of the pumps.
Turbine Blades Call for Innovative Metering, Mixing and Dispensing
After the vacuum supported resin infusion process used to introduce two component resin into fiber matting during the production of rotor blades, and de-molding of the two halves, they must be bonded together. Finally, a smooth outer coating finish has to be applied.
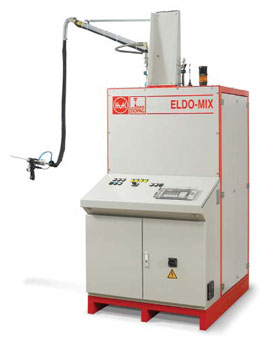
As with the vacuum supported infusion system, one of the most important aspects during the bonding of the two halves is to unsure total accuracy of the mixing ratio. This is a vital point since the life cycle of a wind energy system is directly connected to the mechanical attributes of the rotor blades.
After all, approximately 600 kg of adhesive is applied to the mating surfaces during the bonding process. This procedure must be finished within a defined period, as curing of the mixture must not start before the assembly process is complete.
The ELDO-MIX Glue Resin System, from the Hilger u. Kern / Dopag Group has been especially developed for this purpose and is available as a static or mobile version. The mobile version can be moved parallel to the blade during the application process.
The adhesive is a pasty, thixotropic two component resin with a viscosity of up to several hundred thousand mPa s. The material is sometimes required to have gap filling properties and one or even both components are filled with glass fibers to ensure the stability of the finished product. To reach a satisfactory output rate of 12 l/min (maximum output rate of the ELDO-MIX system is 20 l/min) with these material characteristics, the filling/refilling of the metering pumps must be guaranteed. For this reason, follower plate mounted eccentric pumps are used to feed directly from 200 l drums.
Gel coating is used to protect the rotor blades from environmental conditions and is either applied into the moulds prior to the vacuum supported infusion process or as the final process, following bonding.
The ELDO-MIX Gel Coat System can typically reach output rates of between 2 and 5 l/min. The "A" component, which has a viscosity of approximately 35.000 mPa s, is fed through gear pumps, whilst the "B" component, which has a much lower viscosity of around 3.000 mPa s, uses magnetically coupled axial piston pumps.
The advantage of these types of pumps is that through their design and construction leakage is not an issue, even with speed frequency or back pressure changes. In addition they are hermetically sealed, which is important particularly for the "B" component as the hardener is hygroscopic and can form potentially damaging crystals.
The mixing ratio can be adjusted to suit the application; in this case it is mostly within the range of 100:30 to 100:50, whether working with polyurethanes or epoxy resins. Material is normally supplied by material pressure vessels mounted onto the chassis. During break times, the system is connected to a refilling station where the vessels are automatically refilled directly from 200 l drums.
The Hilger u. Kern / Dopag Group has already installed more than 30 such systems.