Structural Panels Industry
Kirkco offers a large selection of high quality equipment and systems, engineered to meet the needs of our customers. As one of the leading suppliers of metering, mixing and dispensing equipment, our success is built on the understanding of the requirements of dispensing many types of adhesives, mastics and sealants, such as those used within the structural insulated panels industry (SIP).
Get a Quote for a Structural Panel ApplicationStructural Insulated Panels
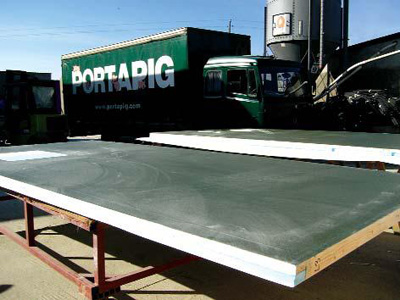
Structural insulated panels are a composite building material. They consist of a sandwich of two layers of structural board with an insulating layer between. The board is usually oriented strand board (OSB) and the foam either expanded polystyrene (EPS), extruded polystyrene (XPS) or polyurethane foam.
Structural insulated panels provide strong structural properties. The rigid insulation core of the SIP performs as a web, while the OSB sheathing exhibits the same properties as the flanges, in much the same way as structural properties of an I-beam or I-column. SIPs replace several components of conventional building construction such as studs and joists, insulation, vapor barrier and air barrier. Typically, structural insulated panels are used for many different applications: exterior wall, roof, floor and foundation systems.
Kirkco offers the highest quality solutions for sstructural insulated panel construction, from accurately meter, mix and dispensing the adhesives onto all types of panels and boxes, to the necessary manufacturing equipment to assemble the completed product. Several application successes include the following:
VARIO-MIX 2A/H
Piston pump driven machine for applying polyurethane adhesives between plywood/foam/plywood in the manufacture of angles.
GP-301
Twin outlet gear pump driven machine for applying polyurethane adhesive to flexible joints.
VARIO-MIX 1A/80
Piston pump driven machine for applying epoxy adhesives to top bridge panels.
D610-200/H
Hydraulically driven piston pump machine for applying mastic beads onto insulation boxes.
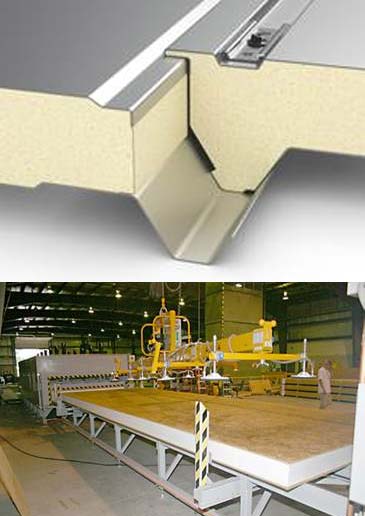
(SIP) Plywood/Foam/Plywood
Used for applying two-component Weiss-USA polyurethane adhesive between the plywood/foam/plywood sandwiches in the manufacturing process of Structural Insulated Panels, Kirkco's GP-301 provides multiple adhesive beads across the entire length of each panel. This electrically driven machine draws material from on-board level controlled pressure vessels. Bunghole pumps are used to feed the materials directly from original 55 Gallon (200-liter) size drums, thus ensuring that the machine is never starved of material. A volumetric metering control system is incorporated into the machine guaranteeing a failsafe supply of mixed material at the selected mix ratio.
Mastic Beads
Dispensing abrasive and highly thixotropic mastic materials require a robust machine of sever duty design and construction whose wetted parts are specially treated to handle these demanding materials.
The DOPAG D610-200/H is a high output piston pump machine that has been developed for this very purpose, delivering uniform mastic beads under any weather conditions.
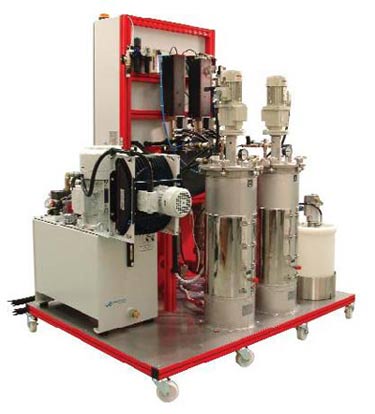
Feeding directly from standard 200-liter size drums, the D610-200H uniquely features two precision metering pumps that both pump and meter the components. Two completely separate hydraulic motors drive the piston pumps, whilst the desired mix ratio and flow rates can easily be selected by using the on-board touch screen controller.
Top Bridge Panel
The VARIO-MIX 1A/80 has been developed to dispense the highly thixotropic two component epoxy adhesives used in the bonding of the top bridge and triplex insulation panels used with the MARK III system.
The machine features variable ratio piston pumps driven by a smooth running pneumatic/oil brake cylinder to accurately proportion and meter the two components prior to dispensing.
A pair of on-board ram mounted drum pumps capable of unloading drums of up to 80 liters in capacity feed the materials into the metering pumps.
A comprehensive heating system ensures that the materials are kept at a constant temperature at all times, whilst all wetted parts are specially treated to withstand the abrasive fillers of highly thixotropic adhesives.
Triplex Membrane
Applying two-component polyurethane adhesive directly onto flexible triplex joints is a process that lends itself to automation by the use of robotic devices that travel the length of the flexible joints while dispensing the mixed material.
A DOPAG ELDO-MIX 202 gear pump driven system provides accurately proportioned material at a constant predetermined temperature, pressure and flow rate. Two separate and independent drive systems supply the adhesive to the two mixing heads, which are mounted directly onto the robotic device.
The ELDO-MIX 202 is compact in size with minimum weight and is built with maximum mobility in mind to allow it to follow the movements of the robot without difficulty.
For more than 30 years the group has developed machines, systems and components to suit your individual needs.
Kirkco is one of the leading solution providers of machines for metering and mixing systems for hot and cold, single or plural component adhesives and polymers, and single component lubricating media such as greases, oils and pastes.
Honeycomb Sandwich Panels
With close to 30 years of experience with dispensing systems, Kirkco provides a solutions approach to the application of epoxy, urethane, silicone, and other specialty adhesives and resins. Utilizing custom turnkey systems developed for the precise application of beads or measured shots, high or low volume pours with or without vacuum. Kirkco is a leader of precision dispensing machines, adhesive dispensing equipment, and custom plural component metering, mixing, and dispensing application solutions involving Honeycomb sandwich panel production.
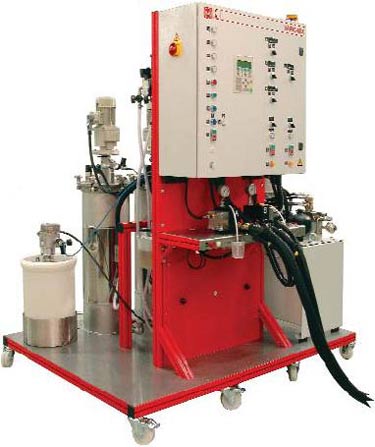
Honeycomb sandwich panel are available in a wide range of configurations. Kirkco's two-component, meter/mix/dispense equipment Used for applying, spraying, roll coating, bead dispensing, two-component Weiss-USA adhesive between the skin/honeycomb/skin material in the honeycomb sandwiches panel manufacturing process. The panel skin materials range from aluminum alloy, to woven or unidirectional fiber glass or carbon fiber webbing. The honeycomb core can be aluminum or non-metallic material. Many benefits can be designed into a panel, but fundamentally all honeycomb sandwich panels offer outstanding stiffness and strength for low weight. Thin, high strength skins are separated by, and bonded to, thick lightweight honeycomb cores; the thicker the core, the higher the stiffness and strength of the panel - for minimal weight gain.
Kirkco offers several solutions for applying the two-component epoxy, urethane, silicone, and other specialty adhesives and resins used in Honeycomb sandwich panel construction. We can bond outer skin to the honeycomb center manual or automatically, applying, spraying, roll coating, bead dispensing, two-component adhesive or reactive resin materials between the skin, if necessary, seal and closed-off edges with filler, extrusions or laminates. Bonding inserts and individual panel joints into assemblies or extrusion. We can provide simple and very effective fabrication process solutions for bonding two-component adhesives in the honeycomb sandwich panel construction.
Honeycomb sandwich panels have been used extensively over the years, for applications where their stiffness/weight and strength/weight benefits cannot be beaten, e.g.
- Aircraft Flooring: Almost all modern aircraft designs have honeycomb sandwich flooring
- Aircraft Interiors: Fitted in nearly all modern aircraft
- Tooling Industry: For lightweight backing structures of checking fixtures and models.
- Ship Interiors: Increasingly, new ships are designed for higher speed and demand lower weight paneling and furnishing
- Train Interiors: The development of high speed and light rail vehicles results in low-weight requirements for paneling and furnishings.
- Marine Industry: Boat stringers and Interior walls.
- Construction: For lightweight cladding and support for stone veneers, etc. reducing overall construction time due to easier handling and lower building structure costs.
Many other applications ranging from the Automotive Industry, Art Restoration, to Electronics HI-FI speaker cabinets and machine parts.