Liquid Paint & Coating
Kirkco single and multiple-component coating solutions improves productivity, reduces operating and maintenance costs and sprays the highest quality finishes and coatings in the harshest environments. Our goal is to take the guesswork out of selecting the right pump, spray package or proportioner for your Spraying and Coating application and provided value through intensive customer support by solving the most difficult coating needs. We always find the optimal solution for a customer's application. This intensive cooperation in all phases of a project, coupled with broad expertise, creates lasting value for the customer that only a reliable solution can provide.
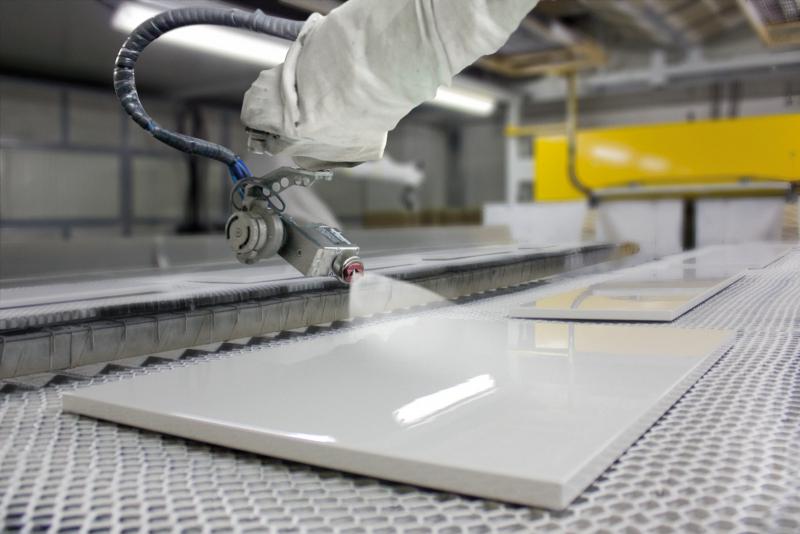
Whether applying multiple-component paints or coatings, transferring liquids, or fighting rust and corrosion, Kirkco would be pleased to offer our assistance as your source for the high performance fluid handling equipment that is specifically designed and engineered with the solution in mind.
Contact Us For Help Finding The Right Paint and Coating System For You
Liquid Application
Writing implements, TV housings, cell phones, laptops and commercial vehicle bodywork, as well as kitchens, wheel rims, yachts and cranes all have something in common? These products and many more are coated using some of our systems and components. Depending on the particular requirements and the environment in which a customer's products will be used, a wide variety of materials can be employed, such as top coats, primers, release agents, adhesives, corrosion protection and more - with either water or solvent based materials.
To be able to process this broad range of materials, we offer components and systems precisely tailored to the requirements of each individual customer. We are one of only a few suppliers to offer the full spectrum of products and technologies needed throughout the entire process chain - from material feeding and mixing to transporting and controlling and, finally, to application of the material on the surface.
Efficient use of resources, maximum quality and economy is what we stand for in everything we do.
Powder Application
Kirkco provides user-friendly, economical and environmentally sound - WAGNER industrial powder coating systems and components. With a focus on continuing research and development and numerous innovations and improvements, WAGNER has had a major impact on the advancement of powder coating technologies for more than 25 years.
This is why WAGNER is able to guarantee its customers reproducible coating results of exceptional quality - even in the case of complex, fully automated processes and unusually shaped coating objects.
Customers around the world rely on our know-how in application techniques, motion and control engineering, powder logistics and booth and recovery technologies.
Container to Spray Gun
Paints, stains, release agents, primers, adhesives and chemicals, whether they have a high or low viscosity, are watery or have a high solid content - they all must pass from the container (can, drum, etc.) to the spray gun. In addition, the material must arrive at the spray gun at a certain pressure. These demands are met by pumps and pressure tanks, which can be differentiated into:
- Piston Pumps
- Diaphragm Pumps
- Pressure Tanks
- Ram Pumps
In addition, a special technology called the hot-spraying method lowers material viscosity by heating the substance. This leads to an optimized spraying pattern and more consistent processes.
Pumps feed the materials through piping and hoses from the container to the spray gun. The entire assembly of this type of system, i.e. the pumps and feed lines, is called the paint supply system.
Paint Supply System
A simple paint supply system consists of a pump and the associated feed lines to the application device. To avoid having to interrupt production in order to change the color or material, a paint supply system can contain, depending on the required scope, a multitude of pumps and piping systems suitable for a large number of different processing materials, colors and application methods.
For a complex paint supply system of this magnitude, it is advisable to have an overall plan drawn up for the entire system that takes into account any special requirements. The material is applied to the work-piece at the outlet of the paint supply system. Various application processes are available for this purpose.
Feed Methods
Material feed methods can be differentiated into two different types: pumps and pressure tanks. Pumps, in turn, are subdivided into piston pumps and diaphragm pumps. A special type of pump is the so-called ram pump for particularly viscous materials such as greases and adhesive and sealants. Piston pumps draw the material out of the container and apply the necessary pressure to push it through hoses or pipes to the spray gun. Most piston pumps offered by Kirkco are pneumatically operated, however, hydraulically driven pumps are available when required for certain applications. Piston pumps are classified by pump ratio and volumetric flow. They are suitable for low to high viscosity materials and flow rates.
In diaphragm pumps, the material is drawn out of the container via a double diaphragm and fed through hoses or pipes to the spray gun with the necessary pressure. All Wagner diaphragm pumps are double membrane pumps characterized by a material feed with very low pulsation and can be grouped into simple double diaphragm pumps, ratio double diaphragm pumps and high pressure double diaphragm pumps.
Pressure tanks accomplish several tasks at once. They feed material by means of compressed air that puts the contents under pressure. The supply of material from a pressure tank is absolutely free of pulsation and continuous. In addition, the pressure tank acts as a material storage facility.
Increasing a material's temperature lowers its viscosity, an effect that can normally only be achieved by thinning the material with a solvent. A further benefit of hot spraying is that the processing temperature remains constant because the material is not subject to temperature fluctuations at the workstation. This helps ensure consistent result.
This special type of piston pump is used with materials of very high viscosity for which the suction of conventional pumps is insufficient, such as greases, lubricants, sealants, adhesives, etc. In ram pumps, the material is fed into the pump by means of pressure and/or a scoop piston. The pump then feeds the material to the spray gun with the necessary pressure.
Spray Coating Definitions and Technology
Transfer Efficiency
Transfer efficiency rates the spray painting equipment's ability to put material on the target, compared to how much escapes as over-spray, bounce back material. Transfer efficiency relates directly to material savings and environmental compliance.
Flow Rate
Flow rate is the volume of material that can effectively be atomized through an applicator. It is typically referred to in ounces per minute (oz./min.) or grams per minute (g./min.)
Air Spray
Air spray is the most widely used finishing method because of its ease of use, flexibility and ability to produce fine, smooth finishes. It is used for the application of low to medium viscosity fluids for products requiring a high quality, Class A or decorative finish. Air spray is typically used in automotive, wood and metal finishing operations that require superior finish quality, typically utilizing atomizing air pressure of 60 psi and fluid pressures in the range of 5-20 psi at the gun.
High Volume Low Pressure (HVLP) Spray
HVLP is a controlled air spray technology that limits the air pressure in the air cap in order to reduce bounce-back and over-spray. Although HVLP guns come very close to achieving the finish quality of air spray, atomization is generally more coarse when working with higher viscosity fluids and higher flow rates. HVLP is typically used on wood and metal finishing and touch-up applications utilizing up to 10 psi atomizing air pressure and fluid pressures in the range of 5-20 psi.
Electrostatic
Electrostatic technology can be applied to air spray, air-assisted and airless spray methods. Electrostatic applicators greatly reduce over-spray while providing better film coverage than non-electrostatic applicators. Electrostatics are commonly used in automobile, aircraft, heavy equipment manufacturing and metal finishing. Kirkco offers both air spray and air-assisted/airless electrostatic spraying equipment.
Air-Assisted
Air-assisted atomization is a hybrid application method that combines the hydraulic atomization method of airless with the atomization of air spray. The result is an atomization level between air spray and airless. This process is ideal for many finishing and coating applications that require high production levels and a relatively smooth finish, such as wood furniture topcoats, fabricated metal parts and farm and construction equipment. Air-assisted atomization typically utilizes air pressures up to 35 psi and fluid pressures range from 250 to 4000 psi at the gun.
Airless
Airless atomization is accomplished by directing fluid under high pressure through a controlled orifice. Airless works best when used to quickly apply high volumes of coatings to large surfaces, such as bridges, storage tanks, or large sheets of metal. Airless is most often used to apply protective, rather than decorative coatings. Typical fluid pressures are up to 5000 psi at the gun.