Dosing Inspection System
Dosing Inspection System (SOMA DIS-C)
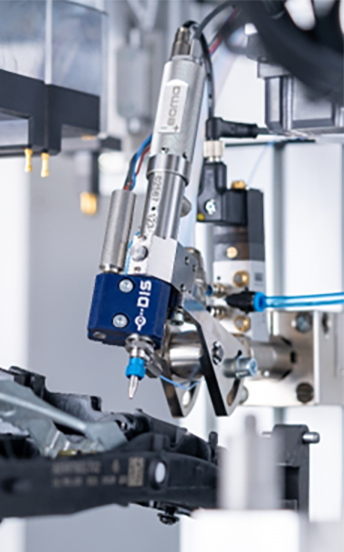
Reproducible quality poses the greatest challenge in industrial lubricant dosing. Impurities or air inclusions in the lubricant can disrupt the dosing process, resulting in poor outcomes.The innovative DIS Dosing Inspection System by SOMA offers automatic and reliable detection of subpar dosing results, enabling prompt corrective actions.
Benefits
- 100% real-time monitoringof dosing impulses on the SOMA IDV Impulse Dosing Valve.
- Utilizes patented process monitoringvia a piezo pressure sensor on the nozzle output.
- Configurable through a web interfacefor digital I/O signal to higher-level control units.
- Automatic determination of positionin the process using teach mode.
Application
The SOMA DIS Dosing Inspection System is ideal for customers with stringent requirements regarding dosing process quality and traceability. In addition to digital I/O evaluation, the system backs up all measured data, saving it to an external FTP server via TCP/IP.
Function
The system monitors the pressure profile in the nozzle using a piezo pressure sensor. Nominal values for maximum pressure, average pressure, and pressure time integral are established beforehand using teach mode. These values are then monitored in real-time by the evaluation electronics and transmitted to the higher-level control unit. All configurations and settings can be conveniently managed via a front-end interface.
SOMA DIS-C Dosing Inspection System
Complete evaluation electronics for SOMA DIS Dosing Inspection System. Unit excludes sensor and cable set.
- Fully automatic interrogation of dosing via the SOMA IDV Impulse Dosing Valve utilizing a piezo pressure sensor in real-time.
- Teach mode and editable process parameters are easily managed through a front-end web interface.
- Evaluation can be conducted using digital IO or via TCP/IP, providing comprehensive dosing traceability data.
- Each SOMA IDV Impulse Dosing Valve requires one system, along with the utilization of valve heating (SOMA IDV-H) and dosing piston stroke monitor (SOMA IDV-INI).
- The SOMA IDV-PVF fast switch valve is necessary for 100% real-time interrogation at a 20 Hz dosing frequency.
- Maximum cable length between the SOMA IDV Impulse Dosing Valve and SOMA DIS evaluation unit is 3 m. The scope of delivery includes the SOMA IDV-D2 nozzle adapter with an adapter for the sensor.
- Wiring harness includes a sensor cable, connection to IDV-PVF (control of SOMA IDV Impulse Dosing Valve), connection cables to higher-level control unit (D-SUB), connection cable for SOMA IDV-INI, and a bridge between booster and evaluation electronics. All cables are 3 m in length.
The Dosing Inspection System by SOMA offers intelligent monitoring of Impulse Dosing Valve dosing processes, providing automatic, verifiable, and real-time oversight. In the realm of industrial lubricant dosing, ensuring reproducible quality poses a significant challenge. Impurities or air inclusions within the lubricant can adversely affect the dosing process, leading to subpar results. SOMA's unique DIS Dosing Inspection System addresses this challenge by automatically and reliably detecting poor dosing outcomes, allowing for appropriate intervention.
The system offers several benefits, including 100% real-time monitoring of dosing impulses on the SOMA IDV Impulse Dosing Valve. It utilizes a patented process monitoring approach with a piezo pressure sensor on the nozzle output. Configurable via a web interface digital I/O signal to the higher-level control unit, it also features automatic position determination in the process through a teach mode. Ideal for customers with stringent requirements for dosing process quality and traceability, the SOMA DIS Dosing Inspection System is recommended. In addition to digital I/O evaluation, the system archives all measured data, saving it to an external FTP server via TCP/IP.
Functionally, the system monitors the pressure profile in the nozzle using a piezo pressure sensor. Beforehand, nominal values for maximum pressure, average pressure, and pressure time integral are taught using the teach mode. These values are then monitored in real-time by the evaluation electronics and transmitted to the higher-level control unit. All configurations and adjustments are facilitated through a front-end web interface.
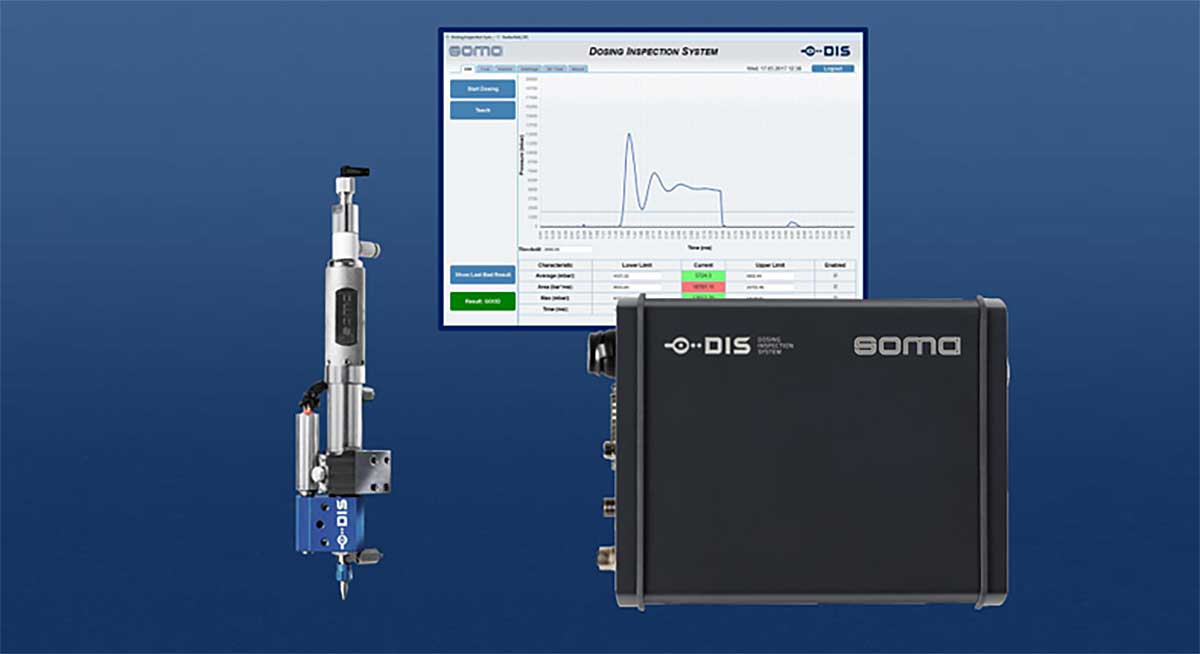