Gel Coat
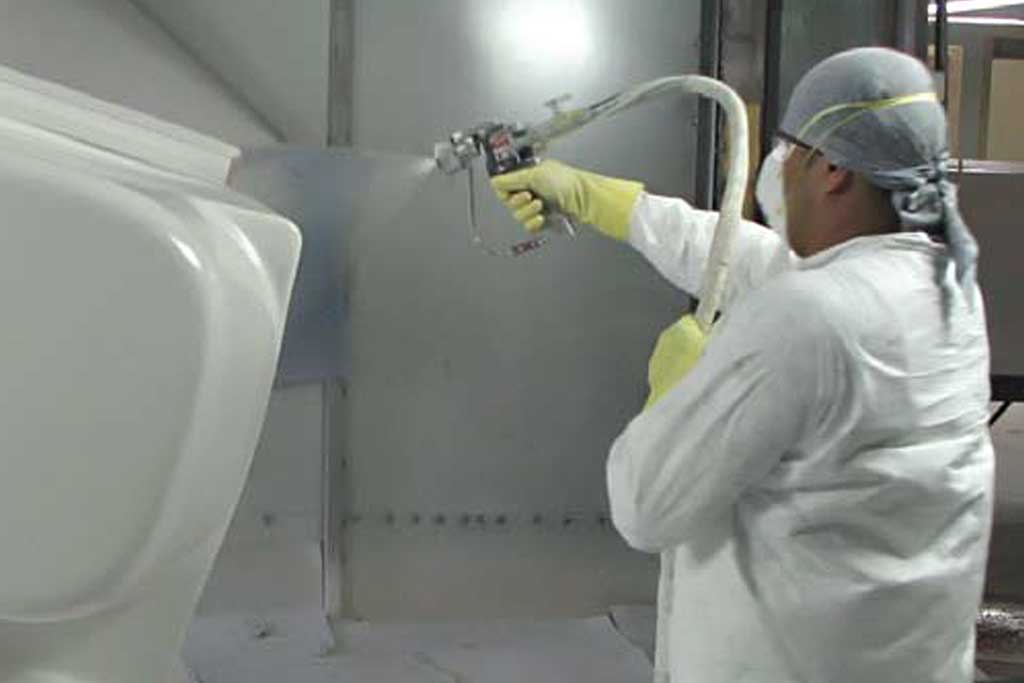
The durability of a composite part heavily relies on the quality of its exposed surface. To protect this surface, a resin-rich layer, typically in the form of a gel coat, is applied. Formulating and applying the gel coat require special attention, as it serves as a crucial part of the laminate and is also the most vulnerable.
Thorough mixing of the gel coat, especially when adding catalyst, is essential to ensure even curing. Inadequate catalyst dispersion can result in uneven gel coat cure, affecting its physical properties. Similarly, improper mixing of pigment can lead to surface imperfections, diminishing the molding's appearance. It's advisable to use pre-pigmented gel coats whenever possible, and low-shear agitators and mixers help minimize mixing issues.
Gel coat application can be done via brush or spray, with advancements in technology favoring the latter. Regardless of the method, it's crucial to use a gel coat specifically formulated for the chosen application technique. Controlling gel coat thickness between 0.4mm to 0.5mm is vital for optimal performance, with a recommended gel coat mixture of 450g-600g/m2.
Ensuring uniform cure is critical to avoid issues like cracking, crazing, or uneven surfaces. Maintaining workshop and material temperatures above 65ºF (18ºC), using a medium reactivity MEKP catalyst at a 2% addition level, and extracting styrene fumes in deep molds are essential practices.
Once the gel coat has cured adequately, the next step in the contact molding process is to apply the backing laminate. A simple touch test can determine the gel coat's readiness for laminating, with commencement ideally within five hours of readiness.