Hand Lay Up
Hand lay-up is a meticulous process integral to composite manufacturing, often employing chopped strand glass fiber mat as the primary reinforcement for contact molding, though the utilization of woven and combination materials has seen significant growth. To initiate, tailored reinforcement 'packs' designed specifically for the mold are prepared, optimizing efficiency and minimizing material wastage. Resin requirements are meticulously calculated by weighing the chosen reinforcement, with recommended resin-to-glass ratios varying depending on the material utilized. After adequate gel coat curing, a liberal application of resin is evenly distributed, followed by firmly pressing the first glass layer into place to ensure thorough consolidation. Impregnation of the reinforcement, crucial for conformity to mold contours, can be achieved using either a brush or roller, with care taken to maintain the fibers' random nature. Consolidation of the laminate, facilitated by various roller types, is imperative for eliminating trapped air bubbles.
Subsequent layers of resin and reinforcement are added until the desired thickness is achieved, with careful attention paid to prevent excessive exotherm, which could lead to defects. Strengthening techniques, such as incorporating reinforcing ribs or metal inserts, are strategically employed as needed. Joining reinforcements to cover the mold surface is accomplished using butt or lap joints, with meticulous attention to detail to ensure seam integrity.
Lastly, surface texture enhancement options, including incorporating a surface tissue or applying a formulated flow coat, are available to achieve desired finish characteristics, offering both smoothness and pigmentation options if required. Hand lay-up, with its detailed processes and material considerations, remains a cornerstone in composite manufacturing, enabling the creation of high-quality, customized components tailored to specific applications.
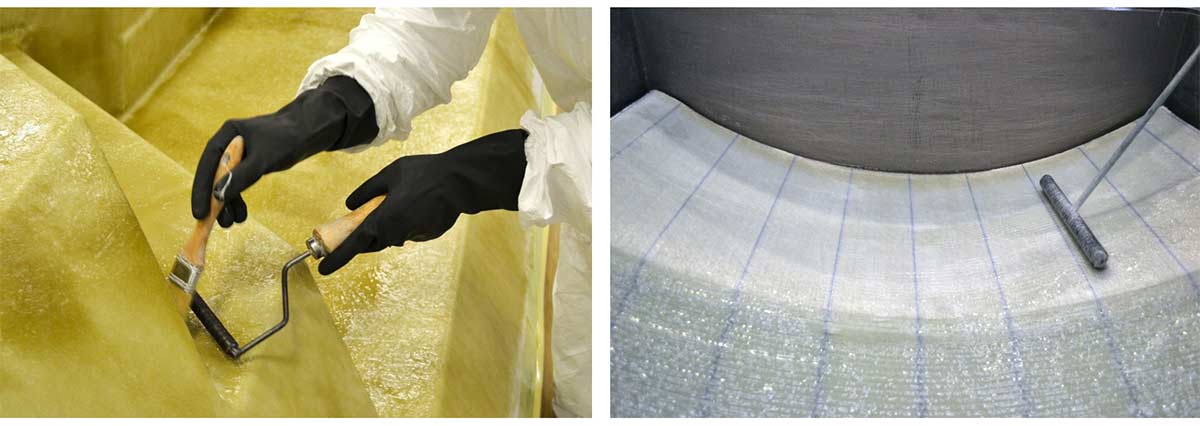