Open Mold Technology
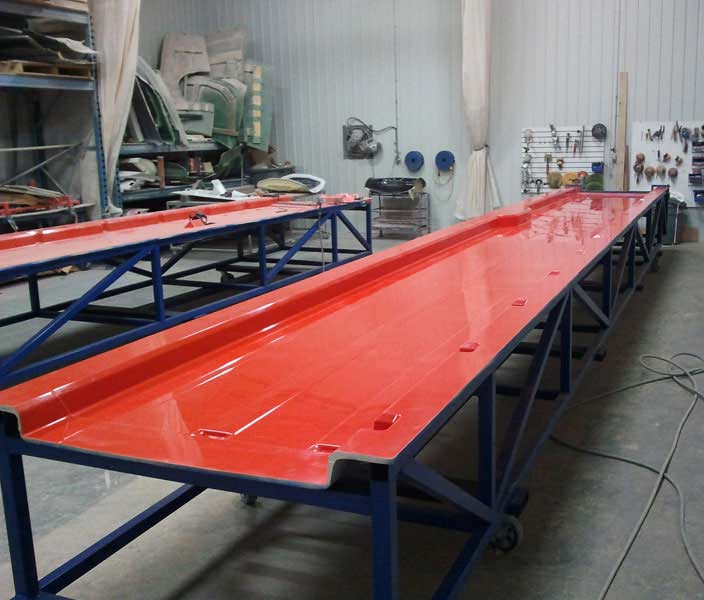
The open mold process, a widely employed technique in composite manufacturing, involves the creation of composite parts within an open cavity mold. This method offers versatility and adaptability across various industries, from aerospace to automotive and marine sectors. The process initiates with the preparation of the mold, typically constructed from materials like fiberglass, carbon fiber, or metal. Surface treatment of the mold with release agents ensures easy removal of the finished part. Next, the chosen reinforcement material, such as fiberglass or carbon fiber fabric, is precisely laid within the mold cavity. This step allows for customization in terms of fiber orientation and ply arrangement, optimizing the mechanical properties of the final product. Subsequently, the resin matrix, often a thermoset like polyester or epoxy, is carefully applied, either manually or through automated methods, to impregnate the reinforcement material thoroughly. This impregnation process is crucial for ensuring uniform distribution of the resin, which ultimately dictates the structural integrity and performance of the composite part. Once the mold is filled, the composite undergoes a curing process, typically involving temperature and pressure control, to facilitate polymerization and solidification of the resin matrix. After curing, the composite part is demolded, trimmed, and finished as necessary to meet desired specifications. The open mold process offers advantages such as scalability, cost-effectiveness for low to medium production volumes, and the ability to produce complex geometries with relative ease. However, it also requires skilled labor for precise material placement and resin application, as well as careful mold maintenance to ensure consistent part quality. Overall, the open mold process remains a cornerstone of composite manufacturing, offering a balance of flexibility and performance across a diverse range of applications.