Vacuum Infusion Molding
Vacuum Infusion Molding: Engineered for Excellence
Kirkco composite Systems offer technologically advanced, durable, and long-lasting solutions for vacuum infusion molding. Our industry-proven components ensure consistent curing, resulting in high-quality parts and end products.
Why Choose Vacuum Infusion Molding?
Precise Material Distribution: Achieve uniform resin distribution for flawless composite structures, reducing defects and voids in your final product.
Exceptional Strength-to-Weight Ratio: Create lightweight, high-strength composite parts ideal for weight-critical industries like aerospace and automotive.
Complex Geometries: Easily manufacture intricate, complex shapes, unlocking new design possibilities.
Environmentally Friendly: Minimize resin waste and emissions, making vacuum infusion molding a sustainable choice.
Vacuum Infusion Molding Process
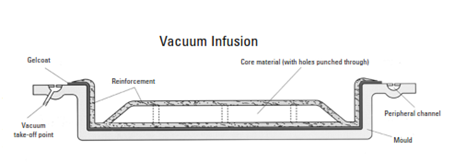
This process can be introduced to a molding shop with minimum investment. Existing open molds can be used with little or no modification, and the process is adaptable to large or small components. In the Vacuum Infusion Molding process, dry reinforcements are encapsulated between a rigid, airtight mold and a flexible membrane (vacuum film or ‘bag’) which is sealed around the edge of the mold. This forms a cavity which is then placed under vacuum to compact the reinforcement.
Catalyzed resin is introduced into the cavity and the vacuum pulls it through the reinforcement. Once the component is fully infused through the material, it cures. after which the bag and the component are removed from the mold.
Resins for use in the Vacuum Infusion Molding process need to be low in viscosity and may also require controlled exothermic properties, for larger sections or thicker components. There are several variants of the Vacuum Infusion Molding process.
Closed Mold Vacuum Infusion
Introduce vacuum infusion molding to your shop with minimal investment. Existing closed molds can be used with little or no modification, making this process adaptable for both large and small components.
The Closed Mold Vacuum Infusion Process
- Layup: Dry reinforcements are placed within a closed, airtight mold.
- Bagging: A vacuum film or 'bag' seals the mold's edge, creating a cavity.
- Resin Infusion: Catalyzed resin is introduced into the cavity, pulled through the reinforcements by vacuum.
- Curing: After full infusion, the component cures, and the bag and part are removed from the mold.
Key Considerations for Vacuum Infusion
Resins used in vacuum infusion should have low viscosity and may require controlled exotherm properties for larger or thicker components.
Explore Vacuum Infusion Molding Today
Welcome to the world of advanced composite manufacturing, where innovation meets precision. Vacuum infusion molding is a cutting-edge technique revolutionizing composite production. This guide explores its applications, benefits, and why it's a game-changer across industries.
Applications of Vacuum Infusion Molding
- Aerospace: Produce lightweight, high-strength components for aircraft, spacecraft, and drones.
- Automotive: Manufacture lightweight composite parts, reducing fuel consumption while maintaining structural integrity.
- Marine: Create strong, durable hulls, decks, and components for harsh marine environments.
- Wind Energy: Craft aerodynamic wind turbine blades for maximum energy generation.
- Architecture: Innovate building facades, interior structures, and decorative elements.
- Sports Equipment:Produce high-performance, lightweight products such as carbon fiber bicycles and tennis rackets.
The Vacuum Infusion Process
- Preparing the Mold: Clean and prep the mold for easy demolding.
- Layup: Place dry reinforcing materials according to the desired design.
- Bagging: Seal the structure with a vacuum bag, creating a vacuum-tight environment.
- Resin Infusion: Introduce liquid resin through controlled vacuum infusion.
- Curing: Cure the part under controlled conditions, ensuring resin hardening.
- Demolding and Finishing: Carefully remove and finish the composite part to specifications.
Elevate Your Manufacturing with Vacuum Infusion Molding
Whether in aerospace, automotive, marine, or high-performance industries, vacuum infusion molding offers precision, strength, and design versatility. Unlock the potential of this advanced technology, elevating your manufacturing processes to new heights of innovation and performance.
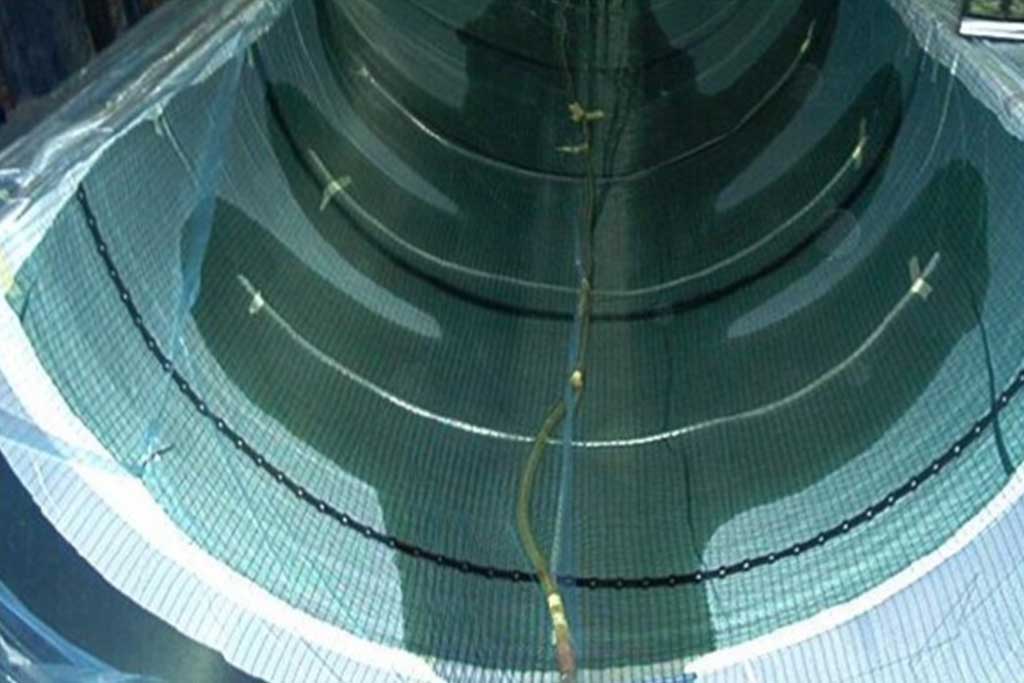