Vario Mix
DOPAG VARIO-MIX® Piston Type Metering and Mixing
The VARIO-MIX® is suitable for use with low to medium high viscosity materials whether they are filled, abrasive, or neither. The VARIO-MIX system can process practically all multi-component polymers and adhesives.
Contact Us For Help Finding the Right Vario-Mix Solution For You
Models
Vario-Mix A
Used for medium to large continuous material output applications such as casting, coating and gluing. The VARIO-MIX A1/A2 uses positive displacement reciprocating metering pumps and drives them by either a pneumatic or hydraulic power supply system attached to an adjustable lever system assembly. The mixing ratio is adjustable within the given range of the selected metering pump combination via a knurled knob. Variable ratios of 1:1 to 20:1 are most common. Mix ratios outside of this range are possible in some situations.
Contact Us For a Vario-Mix A Quote
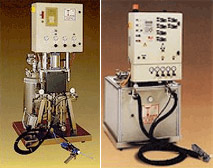
Vario-Mix S
Used for shot dispense applications and is particularly suitable if the material is being processed in larger quantities by hand or in conjunction with an automated system. The VARIO-MIX S1/S2 is available in both pneumatic and hydraulic versions and operates using positive displacement shot metering pumps.
Mix ratio, shot size and cycle speed are designed into the system during configuration. Shot size selection can be from a mechanical or electronic selector or from an onboard MR-20 processing computer or PLC.
Contact Us For a Vario-Mix S Quote
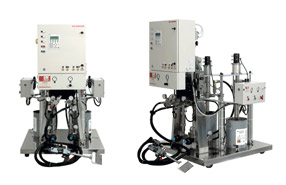
Vario-Mix L (Lamination)
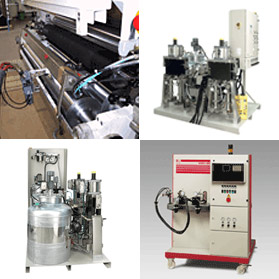
The VARIO-MIX L is an amended design for supplying lamination systems with continuously metered, mixed, and monitored material. This type of system is principally used in the intermittent production and multi-shift operations of the laminated plastics and foil industry.
It operates in the same manner as the VARIO-MIX A with the added features of auto tank refilling, system and material heating and real time close looped monitoring of the material as it is being processed.
All configurations of the VARIO-MIX are standard as “SOLVENT FREE” which means they work as standard without a flushing agent by using disposable static mixers. A version with a low flushing agent requirement is available for special applications if required.
Contact Us For a Vario-Mix L Quote
Vario-Mix Metering and Mixing System Features
-
Basic Construction
A closed circuit is the basis of this concept. It allows the system to shut down for days without removing any crystallised material on the restart. The reaction with air, especially in countries with high atmospheric humidity, is almost impossible because of pressure tanks.
-
Mixing ratio
Variable adjustable
-
Metering control
Independent electronic volume counters permanently monitor the material flow from the metering pumps.
-
Application temperature
The adhesive gradually reaches the application temperature by different heating circuits. Therefore a harmful overheating of the adhesive is avoided.
-
Environmental compliance
The Vario-Mix system operates completely solvent free with static plastic mixer tubes for disposal. The mixed material in the plastic mixer is approximate 10 cm 3, which results in a small quantity of waste material.
-
Quality of the mixed material
The mixer tube in which components A and B are flowing together and the dispensing valve are mounted together on the frame of the laminator machine making the distance of mixed material very short.
-
Maintenance
Very low maintenance and maintenance friendly, automatic refilling, optionally available
-
Level control
There is enough time for a careful drum change due to the refilling system, keeping the pressure tanks always full.
-
Drum change
There is no production interruption, because the refilling is carried out into the 36 l pressure tanks. · In case of a flow rate of 1 l per minute and a mixing ratio of 2:1, the content in the 36 l pressure tanks satisfies for more than 45 minutes to change an empty drum.
-
Refilling pumps
The refilling has no direct impact to the mixing ratio because these pumps are not used simultaneously as metering pumps. The refilling pumps are fed through the bunghole and tightened to avoid air entrance. Therefore a crystallisation of the material is virtually avoided.