Econo-Mix
DOPAG ECONO-MIX® piston type metering and mixing system
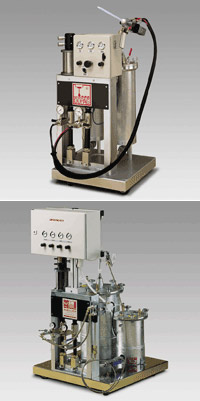
Econo-Mix Metering and Mixing System for low to medium viscosity two-component reactive materials. We characterize the ECONO-MIX by its simplicity in function and design, friendliness of operation and ease of maintenance. This system is a competitive starter model in two-component metering and mixing technology.
This system is capable of processing most reactive polymers, like polyurethanes, silicones and epoxy resins. They can be unfilled, filled as well as slightly abrasive.
The ECONO-MIX unit is a dependable and reliable two component metering and mixing proportioning system that is best used for small to medium production applications. Customization of the base system is available as necessary for the specific application.
The ECONO-MIX is a solvent free, positive displacement piston pump type metering and mixing system, used to handle low to medium viscosity multi component media such as epoxy resins, polyurethanes or silicones with a volumetric mixing ratio of between 1:1 and 6.25:1.
Contact Us For an Econo-Mix Quote
Low pressure feed system such as diaphragm pumps or pressure vessels are used to supply the material into the positive displacement piston metering pumps. Pressure tanks can be mounted onto the machine chassis, or a remote bulk feed unit available for feeding directly from 55-gallon drums.
The pumps are driven by a single air motor. A lever system connects pumps and drive. The pump for the A component is fixed to the lever system and shares the same stroke length as the drive motor. The pump for the B component is adjustable along a lever system providing a variable stroke length, which is used for the fine adjustment of the mixing ratio.
The ECONO-MIX is typically fitted with our standard two component static mixing system that includes a twin snuffer valve combined with a disposable static mixer. The valve contains an infinitely adjustable “snuff back” effect to avoid dripping after metering has finished. Should mixed material be allowed to cure in the mixer, it can be replaced simply and inexpensively, thus avoiding a time consuming, expensive and environmentally damaging solvent flushing cycle.
Optionally we can offer both dynamic mixers and/or dynamic static mixer valves where the material requires an aggressive blending cycle necessary to achieve their proper mix.
Equipment Packages
Standard:
- Portable chassis
- Pressure vessels
- Double acting piston pumps
- Air motor with lever system
- Static mixing system
- Twin snuffer valve
- Disposable static mixer
- Pneumatic-mechanical control
Optional:
- Static-dynamic mixing systems
- Mixing block with static steel mixer
- Pressure vessels in variable sizes
- Level control
- Agitator (electric or pneumatic)
- Heating
- Flushing
- Pot life control
- Material filter
- Material pressure regulator
- Degassing / Vacuum System
Typical Applications:
- Coating
- Gluing / Bonding
- Rapid Prototyping
- Encapsulating
- Potting
Features and Benefits:
- Compact Design: Easy to handle system with continuous output
- Economic Solution: Low cost continuous metering system as an alternative to hand mixing
- Variable Mix Ratio: Pneumatic motor with beam supported pump linkage system
- Variable Output Rate: Continuous flow rate pneumatically adjusted
- Solvent-free Standards: Solvent flush available as necessary
- Manual Operation: Particularly suitable when small quantities are required
- Standard Version: Various options available for customization
- Various Mix Systems: Static, dynamic, static/dynamic
- Bulk Supply/Tanks: Several sizes of pressure vessels