High Pressure Impingement Mixing Valve
Impingement Mixing Valves for Urethane Foam & Elastomer: Enhancing Productivity
Welcome to Kirkco, your trusted partner for advanced impingement mixing valves designed to elevate productivity in both filled and unfilled polyurethane applications. Our high-performance, high-pressure mixing heads stand at the forefront of foam processing units, featuring a precision tight-tolerance plunger design that sets industry standards.
Need Help Finding the right High Pressure Impingement System?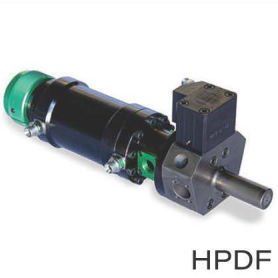
High-Pressure Impingement Mixing Valve: Revolutionizing Polyurethane Processing
How it Works: The High-Pressure Impingement Mixing Valve operates with meticulous precision, ensuring the seamless blending of materials in both filled and unfilled polyurethane applications. During the dispensing cycle, our valve utilizes a recirculation mode, where materials flow through control orifices and recirculation grooves on each side of a precision plunger. This innovative design allows for optimal mixing efficiency before the materials impinge at pressures of up to 3,500 psi, resulting in a smooth and consistent pour into open and closed molds, enhancing the overall quality of your end products.
Applications of Use:Our High-Pressure Impingement Mixing Valve finds its prowess in a diverse range of applications, making it a versatile and indispensable tool in the realm of polyurethane processing..
- Closed Mold Applications: The valve excels in closed mold applications, providing reliable and cost-effective processing for automotive parts, industrial components, and more.
- Open Mold Applications: Tailored for open mold applications, our mixing valve facilitates precise pouring for continuous and discontinuous panel applications, ensuring efficiency in diverse manufacturing processes.
- Spray Applications: The valve's design is optimized for spray applications, making it an ideal choice for industries requiring a high degree of precision in coating and insulation processes.
- Continuous Sandwich Panel Applications: Specifically engineered for continuous sandwich panel applications, our mixing valve contributes to the production of high-quality panels used in construction and other industries.
- Filler/Powder Incorporation: The valve's versatility extends to filler/powder incorporation, allowing for efficient blending of raw materials to meet the specific requirements of your formulations.
Benefits of High-Pressure Impingement Mixing Valve:
- Enhanced Mixing Efficiency: The precision design ensures thorough impingement, leading to improved mixing efficiency and superior product quality.
- Cost Savings: By eliminating the need for cleaning solvents and reducing waste, our mixing valve contributes to significant cost savings in your production processes.
- Fast-Reaction Formulations: The valve's capabilities enable the use of fast-reacting formulations, reducing production cycle times and increasing overall productivity.
Choose Excellence with Kirkco: Experience the unparalleled advantages of our High-Pressure Impingement Mixing Valve. Whether involved in closed mold applications, open mold processes, or specialized applications like spray or filler incorporation, Kirkco's mixing valve solutions are engineered to elevate urethane foam and elastomer production.
Contact us to explore how our innovative mixing valve technology can be customized for your polyurethane processing needs. Trust Kirkco for reliable, cost-effective, and precision-driven solutions that define the future of foam processing.
High-Pressure Foam Mix Heads for Reliable, Cost-Effective Polyurethane Processing:
KIRKCO L-style and straight polyurethane foam mixing heads are designed for high-pressure impingement mixing, offering long life across a wide range of open mold and closed mold applications.
Straight Type Mixing Head:
During a recirculation mode, materials flow through control orifices and recirculation grooves on each side of a precision plunger before returning to the machine tanks. When a dispense cycle is initiated, the plunger, actuated by a double-acting cylinder, retracts, allowing both materials to impinge at pressures up to 3,500 psi (ideal for closed mold applications).
Straight-Style Mix Head Features:
- Ideal for continuous and discontinuous panel applications.
- Compact
- Economical
Explore our rental mix heads, which can be used to try out a mix head with your application or temporarily replace a mix head that needs repair. For more information, contact us
Injector Styles:
Conical Style injectors for rigid and flexible foam applications, including refrigerators, walk-in coolers, furniture, and automotive seat cushions. Choose from a wide range of orifice and needle sizes for optimal mixing and shot control.
Diesel Style injectors for hard-to-mix polyurethane foam applications like steering wheels and acoustical foams. Select from various sizes and spring-adjustment or pin-adjusted holders.
Pneumatically controlled injectors are available for setpoint control or remote adjustment of shot pressures. Let our process experts help you select the correct model and combination of injectors for your application.
High-Pressure Unit Options:
L-Style Mix Head Features:
- Optimum shot control.
- Variety of injector styles and sizes to fit your application.
- Adjustable cleanout piston stroke improves mixing efficiency (standard on every mix head).
- Double cleanout piston seals for longer life.
- Optional recirculating color groove.
- Special nozzle lengths available.
- Double L mix heads with two pour pistons for seating applications.
- High-strength materials and seals for maximum durability.
- Separate cleanout hydraulics from the chemical block to minimize oil contamination.
- Laminar output flow for splash-free operation with open molds.
- 200,000 shots, 1-year warranty.
- Low-cost repairs and seal changes available.
"L" Type Mixing Head: A smaller, horizontal impingement chamber is added to reduce the flow velocity of materials passing through a larger vertical chamber (ideal for open mold applications).
Four Models to Choose From: Straight and L-style Mix Heads:
- HPLF: Axial piston head for closed mold applications.
- HPDF: Dual piston head for open mold applications.
- HPRM: Filler/Powder in raw materials.
- HPSH: Axial piston head for spray applications.
Beyond impingement mixing valves, Kirkco is your one-stop solution for polyurethane manufacturing systems. We design, manufacture, and supply fully integrated systems for insulating foam panels, refrigerators, automotive parts, slab stock, and various other end uses.
Contact Kirkco today to discuss how our impingement mixing valves can transform your production process. Experience the Kirkco difference in precision, efficiency, and reliability.